
New Development Based on High-Sensitivity Nivio xMR SensorMeasurement of Weak Magnetic Fields
from Minute Areas Possible
Migne Compact, High-Performance Magnetic Sensor
TDK developed a high-performance magnetic sensor that can detect extremely weak magnetic fields by applying the advanced thin-film processing technology developed through manufacture of HDD heads. This new sensor can be used in inspections for metallic foreign material on manufacturing and inspection lines, contributing substantially to enhancing the quality of pharmaceutical and chemical industry products as well as lithium-ion batteries, fuel cells, and many other products.
Based on the technology used in the Nivio high-sensitivity magnetic sensor, which was the first sensor capable of measuring weak cardiac magnetic fields at room temperature, TDK created the Migne compact, high-performance xMR sensor, which makes possible high-efficiency, contactless detection of minute metallic foreign material (including iron and stainless steel) smaller than 100 µm, which could not be detected by earlier inspection devices. Use of the sensor will reduce the risk of contamination by minute metallic foreign material in manufacturing processes for pharmaceutical products and chemical industry products as well as electrode materials and separators for lithium-ion batteries and fuel cells and many other products, greatly increasing product safety, reliability, and lifespans.
- An ultrahigh-sensitivity magnetic sensor that applies the spintronics technologies acquired from HDD head technologies.
- A more compact and lower-profile sensor achieved based on the Nivio high-sensitivity magnetic sensor, which can measure weak cardiac magnetic fields at room temperature.
- Uses magnetization to detect magnetic metallic foreign material (including iron and stainless steel) tens of micrometers in size, which can be difficult to detect using x-ray inspection machines. Can also detect magnetized iron rust (magnetite: Fe3O4; and maghemite: γ-Fe2O3).
- Can greatly reduce the risk of contamination by magnetic metallic foreign material in pharmaceutical products and chemical industry products as well as electrode materials and separators for lithium-ion batteries and fuel cells and many other products.
- Operates on direct current voltage (USB power supply) and achieves a high signal-to-noise (S/N) ratio for detecting minute magnetic fields.
- Can also be used to detect minute magnetic fields over a wide area through arraying or scanning.
- 1Types and Principles of Foreign Material Inspection
- 2X-Ray-Inspection Machines and Metallic Foreign Material Detectors Are the Mainstream
- 3Iron and Stainless Steel Particles Are the Main Targets
- 4Various Types of Magnetic Sensors and Their Principles
- 5Reasons Why Minute Magnetic Metallic Foreign Material Are Difficult to Detect
- 6Magnetic Foreign Material Detectors Are Commonly Used
- 7Magnetic Sensors Suitable for Magnetization Metallic Foreign Material Detectors
- 8Fundamental Principles of xMR Sensors
- 9Clear Images of Magnetic Dipoles in Minute Magnetic Particles
- 10Excellent Sensitivity and Extremely High S/N Ratio
- 11Capable of Detecting Minute Stainless Steel Particles Just 20 µm in Size!
- 12Summary
Types and Principles of Foreign Material Inspection
At the manufacturing sites of pharmaceutical product makers, cosmetic product makers, chemical industry product makers, and others, in addition to foreign material that can be seen by eye, meticulous attention is also paid to the adhesion on and contamination of products by minute foreign material that cannot be seen by eye known as contamination or particles. There are various methods of inspecting for foreign material, and they are categorized according to their underlying principles as indicated below.
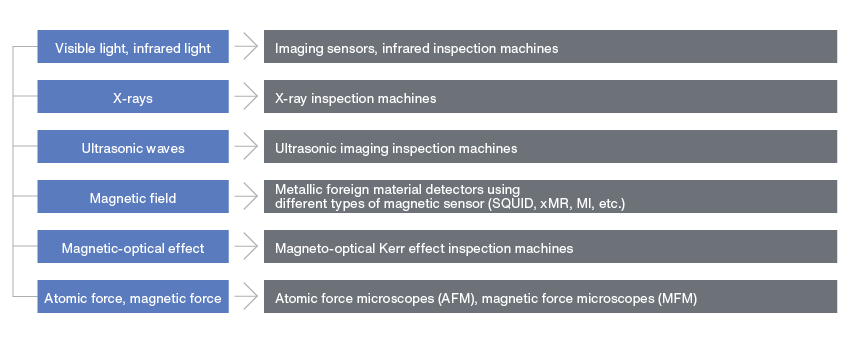
Inspection using cameras, image sensors, and other devices integrates image processing technology, artificial intelligence (AI) technology, and other technologies, becoming increasingly sophisticated. These types of optical inspection devices, however, have the disadvantage of being able to inspect only the surface of products such as the opaque test pieces and products that have already been packaged.
By using ultrasonic waves, it is possible to inspect the interiors of products, but the resolution is limited to the millimeter order, making it difficult to detect minute foreign material. Magneto-optical Kerr effect inspection devices have a narrow field of view and can measure only the surface, and if there is any contamination or surface irregularities, foreign material cannot be detected. Devices such as atomic force microscopes (AFMs) and magnetic force microscopes (MFMs) have high spatial resolution on the order of tens to hundreds of nanometers (10-9 m) and are used in a variety of research applications. The scanning range, however, is limited and sensor sensitivity is low, and as a result, they are not suitable for use in inspection devices in manufacturing industries, which require contactless inspection.
X-Ray-Inspection Machines and Metallic Foreign Material Detectors Are the Mainstream
Currently, x-ray inspection machines are widely used by food, pharmaceutical, and other manufacturers to detect foreign material at the manufacturing site. The products to be inspected are transported by a conveyor belt and exposed to x-rays, and a line sensor detects abnormalities based on the amount of x-ray transmission, enabling the speedy detection of foreign material on the surface or in the interior of products. This method has the advantage of being able to detect metallic foreign material including iron, stainless steel, aluminum, and copper as well as non-metallic foreign material including glass, stone, rubber, plastic, paper, and cloth. The sensitivity of x-ray foreign material inspection machines for metallic foreign material is on the order of several hundred µm, and it is difficult to detect minute metallic foreign material 200 µm in size or smaller using x-ray inspection machines alone. Accordingly, x-ray inspection machines are used along with various other types of metallic foreign material detectors.
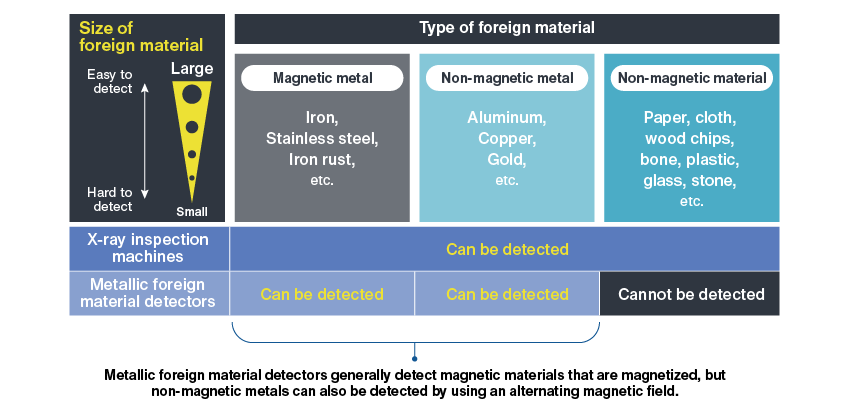
Iron and Stainless Steel Particles Are the Main Targets
Demand for high-performance metallic foreign material detectors that can detect minute metallic particles 200 µm in size and smaller from makers of lithium-ion batteries, fuel cells, and other battery manufacturers is growing. This is because contamination of the main components including electrode materials and separators by minute metallic foreign material can be a cause of heat generation, fire, degradation of battery capacity, and shortening of battery lifespan.
Among the various minute metallic foreign materials, the main targets of detection are magnetic metals including iron and stainless steel. Non-magnetic metals, such as aluminum and copper, are highly viscous and less susceptible to forming minute particles, and it is possible to mitigate the risk of contamination by enhancing the cleanliness of the manufacturing environment. Many manufacturing devices, however, are made from iron and stainless steel, and contamination by particles generated during operation, maintenance, and so on are difficult to avoid even when exercising meticulous care. For this reason, there have been strong calls for high-performance metallic foreign material detectors that can detect magnetic metal particles tens of µm in size or smaller, which until now had been overlooked.
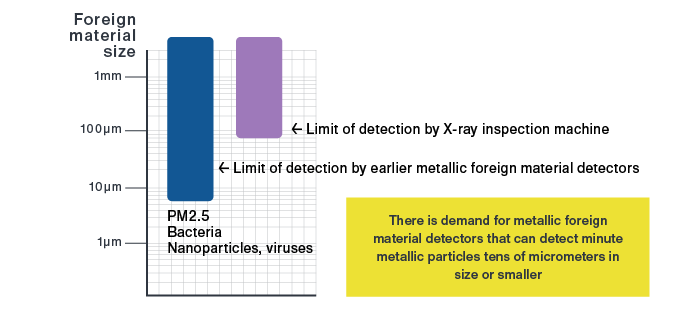
Various Types of Magnetic Sensors and Their Principles
Various types of magnetic sensors are used to measure the magnetic fields of magnetic materials. The sources and strengths of the magnetic fields around us and the ranges of detectable magnetic fields of the main magnetic sensors are indicated below.

The fundamental principles of each magnetic field measurement method indicated in the figure above are described below.
- Search Coil Method (Electromagnetic Induction Method)
- This method uses the same principles as the metal detectors found at airport security gates. When metal passes between an oscillator coil and a receiving coil, eddy currents are generated on the surface of the metal due to the electromagnetic induction phenomenon and the magnetic field changes, and these changes are detected by the receiving coil.
- Hall Element Method
- This method makes use of a phenomenon known as the Hall effect, which causes a potential difference generated by the Lorentz force when an external magnetic field is applied to metal or a semiconductor through which current is flowing. Hall sensors using compound semiconductor, such as GaAs (gallium arsenide) and InSb (indium antimony), are compact and simple magnetic sensors used for many applications.
- Flux Gate (FG) Method
- This is a sensor with a structure in which an excitation coil and a detection coil are wound around a core made from a soft magnetic material with high magnetic permeability. When a magnetic field is applied to the core by the test item, a voltage proportional to the magnetic field strength is induced in the detection coil, and the strength of the magnetic field can be measured.
- Magnetoresistive (MR) Effect Method
- This type of sensor employs the magnetoresistive (MR) effect, which causes a slight change in electrical resistance when a magnetic field is applied to a semiconductor or a ferromagnetic metal. The sensors are used as magnetic sensors to read the magnetic data on tickets used in automatic ticket gates, magnetic ink patterns on banknotes, and other data. In the broad sense, the giant magnetoresistive (GMR) effect sensors and tunneling magnetoresistive (TMR) effect sensors, which are used as the read elements of HDD magnetic heads are types of MR sensors.(For more information on HDD magnetic heads,
see:https://product.tdk.com/ja/techlibrary/productoverview/tmr-angle-sensors.html)
- SQUID Method
- SQUID is an abbreviation for superconducting quantum interference device. A squid sensor is a magnetic sensor in which a Josephson junction is connected to a part of a superconductor coil. They are characterized by ultra-sized sensitivity that can detect cardiac magnetic fields and brain magnetic fields, but a cooling device using liquid helium is necessary to maintain the superconducting condition of the coil.
- Features of TDK’s Nivio and Migne xMR Sensors
- An xMR sensor is a sensor that uses the MR method as the detection method. These sensors, which are marketed under the product names Nivio and Migne, are high-sensitivity magnetic sensors manufactured using advanced thin-film processing technology.
Since they are spintronics-type MR sensors including giant magnetoresistive (GMR) effect sensors and tunneling magnetoresistive (TMR) effect sensors, TDK refers to them as xMR sensors. They feature detection sensitivity on the pT (10-12T) order, which rivals that of a SQUID sensor at room temperature, eliminating the need for a cooling device. Through joint research with the Graduate School of the Tokyo Medical and Dental University, TDK successfully developed a high-sensitivity magnetic sensor that can measure cardiac magnetic fields (2016). Based on this technology, TDK developed the highly versatile Nivio xMR sensor and the more compact Migne xMR magnetic sensor.
Reasons Why Minute Magnetic Metallic Foreign Material Are Difficult to Detect
Of the various magnetic field measurement methods described above, those that can detect extremely weak magnetic fields weaker than the earth’s magnetic field are the FG method, MR method, and SQUID method. However, extremely weak magnetic fields have various aspects that depend on the mechanism and size of the source. For example, the Earth’s magnetic field is extremely weak, but it is nearly uniformly distributed throughout the surface of the earth, and as a result, can be detected even by a compass. The electronic compasses in smart phones use a simple Hall sensor.
The cardiac magnetic field is a magnetic field produced by the bio current flowing inside the heart. It is an extremely weak magnetic fields that is approximately one ten-millionth the strength of the earth’s magnetic field, but it is distributed nearly uniformly throughout the heart, which is about the size of a fist, and consequently, it can be detected from the surface of the body.

In contrast to this, detecting the magnetic fields of minute magnetic metallic foreign material requires measurement by a sensor element that is close to the foreign material. Unlike the earth’s magnetic field or a cardiac magnetic field, the source of the magnetic field is minute and the strength of the magnetic field diminishes rapidly with distance.
The strength of the magnetic field varies depending on the size and shape (spherical, rod -shaped, etc.) of the particle, the strength of magnetization, the direction of the magnetic flux lines, and other factors, and theoretically, as the distance from the magnetic pole increases, the field strength decreases approximately in inverse proportion to the cube of the distance.
To give an example, assume that a single particle of a magnetic metallic object 50 µm in size contaminates a sheet-shaped material. In order to detect the subject, the sensor element must be brought close, within a few millimeters, and the entire sheet must be scanned. This is comparable to locating a single needle buried in a desert, and it is extremely difficult technologically to detect minute magnetic metallic foreign material.
Magnetic Foreign Material Detectors Are Commonly Used
As discussed above, magnetic metallic particles (abrasion dust and powder from peeling) of iron or stainless steel are a problem on the manufacturing lines of many products. The main source is stainless steel manufacturing equipment, but such particles can also be generated by conveying equipment, containers, tools, and other items. For this reason, magnetized metallic particle detectors that use powerful magnets to magnetize these minute magnetic metallic particles and detect them with magnetic sensors are now in widespread use.
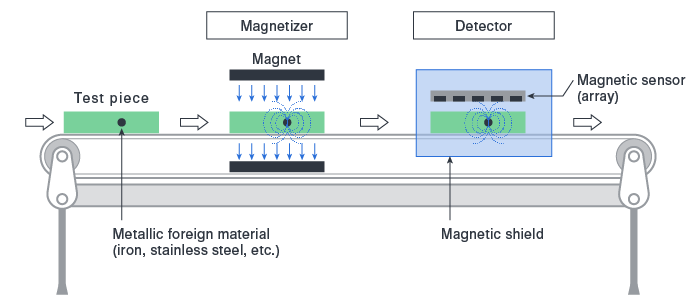
The 18-8 stainless steel (SUS304) used in tableware such as spoons is not attracted by magnets, and stainless steel is generally thought to be a non-magnetic metal, but this is incorrect. Stainless steel is an alloy, of which the main component is iron (Fe) with chromium (Cr) and nickel (Ni), which are iron group elements. It is classified into austenitic, martensitic, and ferritic grades depending on differences in the metallic structure. Austenitic 18-8 stainless steel (SUS304) is a non-magnetic metal that changes its metallic structure when bent, pounded, or ground into pieces, making it attracted by magnets.
Therefore, even though the magnetic susceptibility of stainless steel is not as high as that of iron, it can be detected by magnetic sensors using magnetization. Rusted iron (magnetite: Fe3O4; and maghemite: γ-Fe2O3) that has been magnetized can also be detected.
Magnetic Sensors Suitable for Magnetization Metallic Foreign Material Detectors
What types of magnetic sensors are suitable for magnetization metallic particle detectors that can detect minute magnetic metallic foreign material 100 µm in size or smaller? SQUID sensors have ultra-high sensitivity, but they require a cooling device that uses liquid helium, which causes the equipment to be large, so they are unsuitable. Metallic particle detectors with general magnetic sensors that use other methods are available on the market, but their detection sensitivity is inadequate.
To address this need, TDK developed the xMR type Migne magnetic sensor based on the Nivio high-sensitivity magnetic sensor, the first in the world that can detect weak cardiac magnetic fields at room temperature. By adopting innovations in the magnetic circuit and other areas, the signal-to-noise ratio for weak magnetic fields is even higher than the Nivio high-sensitivity magnetic sensor, and a compact, low-profile sensor just 8 × 8 × 5 mm in size—small enough to fit on the tip of a finger—was created.

Fundamental Principles of xMR Sensors
The fundamental principles of the xMR sensors used in TDK’s Migne sensor are described below. xMR sensors have a multi-layer structure with a thin film of a non-magnetic material sandwiched between thin films of ferromagnetic material. One thin film of ferromagnetic material, which is called the pin layer, has a fixed magnetization direction (pinning), and the other thin film of ferromagnetic material is a free layer that follows the direction of an external magnetic field freely. The electrical resistance of the element varies in proportion to the relative angle of magnetization of the orientation between the pin layer and the free layer, and therefore, the magnetic field strength can be detected from the magnitude of the output current.
xMR sensors feature high-sensitivity on the level of nT to pT (10-9 - 10-12T) and like FG and other sensors, do not require a complicated oscillation circuit. The ability to obtain the signal simply by supplying DC current from the power supply is a major advantage.
Temperature characteristics are extremely important for magnetic sensors that target extremely weak magnetic fields that are weaker than the earth’s magnetic field. The temperature characteristics of xMR elements are excellent, but resistance values change with changes in temperature, although only slightly. In order to minimize this temperature drift, the Migne sensor has four xMR elements manufactured in a bridge structure (Wheatstone bridge circuit) on a substrate, and the voltage differential is used to compensate for temperature. This means that it is necessary to align the characteristics of the four elements, but TDK overcame this problem using its advanced thin-film processing technology, achieving an extremely reliable xMR sensor.
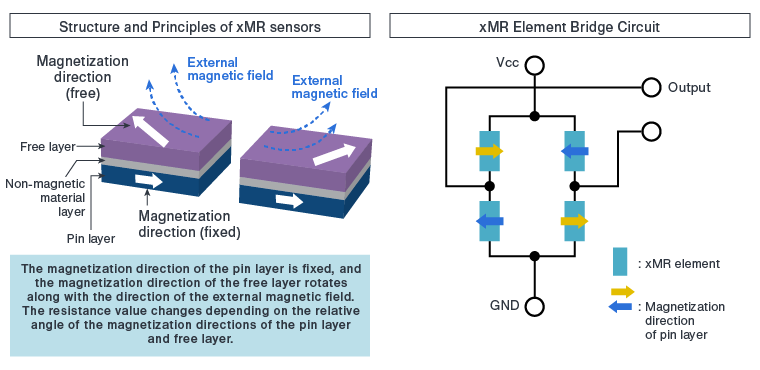
Clear Images of Magnetic Dipoles in Minute Magnetic Particles
The figure below shows images of a minute magnetized iron particle (sphere) as the test piece when magnetized by a magnet and scanned (area 20 × 20 mm) for its magnetic field using the Migne sensor. It can be seen that the magnetized iron particle is a minute magnetic dipole with north and south poles. The red indicates that the repelling direction of the magnetic field lines, and blue indicates the attracting direction of the magnetic field lines.
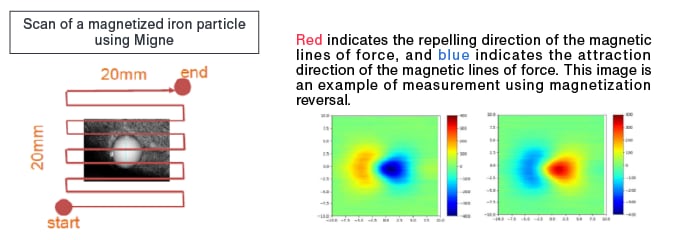
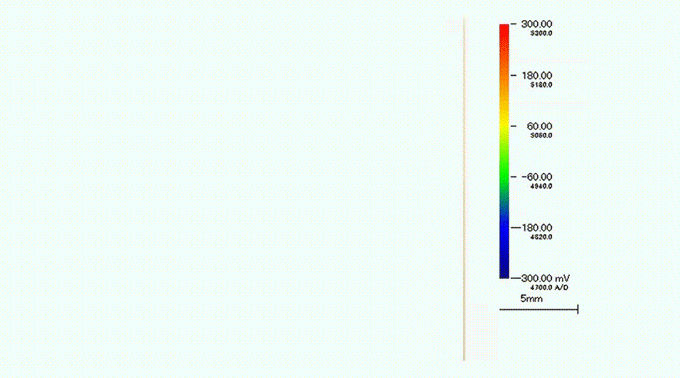
Excellent Sensitivity and Extremely High S/N Ratio
The signal-to-noise ratio (S/N ratio) is important when detecting weak magnetic fields. The magnetic fields of magnetic particles detected by the magnetic sensor are output as signals with steep peaks, but if the signal is concealed by magnetic noise, it is of no use.
The figure below shows images of magnetic field strength on the X-Y surface and X-Z surface of magnetized iron particles (80 µm and 50 µm in diameter) using the Migne sensor. It can be seen that the Migne sensor boasts excellent sensitivity and an extremely high S/N ratio.
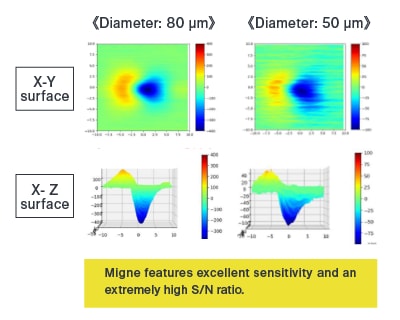
Migne is an xMR sensor based on the Nivio high-sensitivity magnetic sensor, but by making innovations to the magnetic circuit and other areas, the sensor was miniaturized and the performance for detecting minute magnetic metallic foreign material was substantially increased. The figure below shows the results of evaluations of Nivio and Migne SN ratios (test pieces: iron particles 20 µm - 80 µm in diameter with a sensor distance of 2 mm).
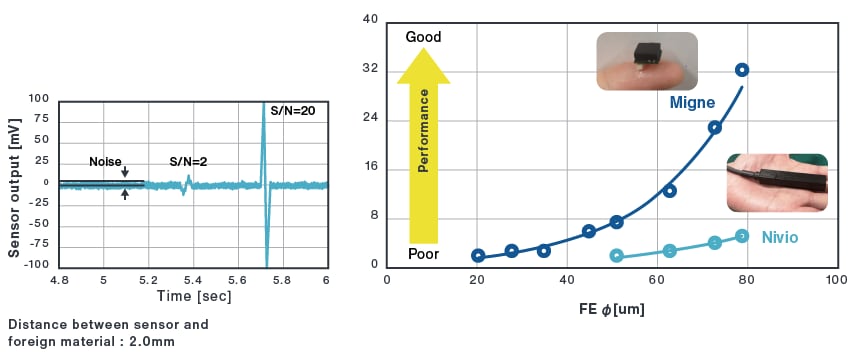
Capable of Detecting Minute Stainless Steel Particles That Were Difficult to Detect with Earlier Devices!
In the case of minute magnetized metallic foreign material, stainless steel is more difficult to detect than iron, but there is high demand for metal detectors that can detect minute stainless steel particles on manufacturing and inspection lines.
TDK’s Migne is a cutting-edge magnetic sensor that can detect minute stainless steel particles that are difficult to detect with earlier detectors.
The figure below shows a magnetized minute stainless steel powder particle sample (40 ×16.6 µm in size) and a measurement image of the magnetic field strength using the Migne sensor. The distance between the Migne sensor and the stainless steel particle is 1 mm. Even though the particle is stainless steel powder, clear images comparable to those of iron particles are obtained.
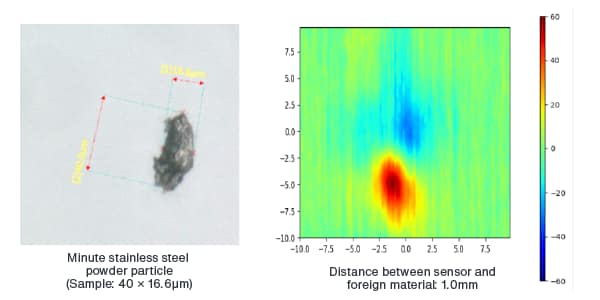
To give a sense of the amazing performance of the Migne sensor, which can detect minute stainless steel powder particles just 40 ×16.6 µm in size and a distance of 1 mm, we prepared a schematic diagram enlarged 100 times. When magnified 100 times, the performance is equivalent to Migne detecting the weak magnetic field of a stainless steel powder particle with a diameter of 2 mm at a distance of 10 cm. Considering that magnetic field strength weakened in inverse proportion to the cube of the distance, it can be understood that Migne is a revolutionary magnetic sensor for detecting magnetic metal foreign material. Migne of course also exhibits excellent detection performance in minute magnetic field detection applications other than foreign material detection.
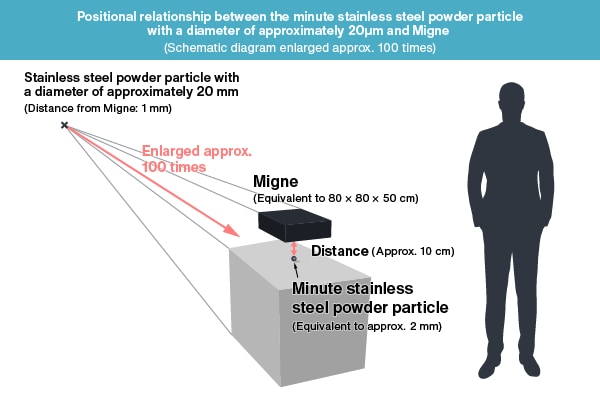
Approximately 20 µm Measured by Migne at a Distance of 1.0 mm (enlarged 100 times)
Summary
Makers of pharmaceutical products, chemical industry products, and other products use x-ray inspection machines along with metallic foreign material detectors, and magnetization metallic foreign material detectors have become the mainstream for detecting minute magnetic metallic foreign material such as iron and stainless steel.
Magnetization metallic foreign material detectors that can detect minute magnetized metallic particles 100 µm in size or smaller must have high sensitivity to detect weak magnetic fields on the nT to pT (10-9 - 10-12T) level as well as compact and outstanding magnetic sensors that can be easily arrayed. TDK’s Migne sensor is a compact, low-profile, versatile, and outstanding magnetic sensor developed based on the Nivio high-sensitivity magnetic sensor, which can measure cardiac magnetic fields. By creating an array out of multiple sensor elements, Migne is able to detect minute magnetized metallic foreign material on the scale of tens of micrometers over a wide range.
Production volumes of the lithium-ion batteries used in mobile devices, robots, drones, electric vehicles (EVs) and many other products are increasing rapidly, and there are strong demands regarding the safety, reliability, and long lifespan regarding those batteries. In addition to use with lithium-ion batteries, we expect that the Migne will be used in detectors for detecting minute magnetized metallic foreign material in the electrode material, separators, and other components of fuel cells and new types of secondary batteries. Migne of course demonstrates outstanding performance not only for detecting foreign material, but in other applications for detecting minute magnetic fields.
TDK is conducting research and development in collaboration with Yokohama National University on magnetic particle imaging devices, which employ diagnostic imaging technology using xMR sensors. Applications for TDK’s xMR sensors are expanding from foreign material detection and manufacturing industries to non-destructive testing and the medical and biotechnological fields (e.g., magnetic field measurement of cell activity), and they hold great potential for the future.
If you have any questions or inquiries regarding the TDK xMR sensors and Migne sensor introduced in this article, please feel free to contact us. We also plan to develop a service for the provision of desktop scanners equipped with the Migne sensor for detecting minute magnetic metallic foreign material.